10 April 2022
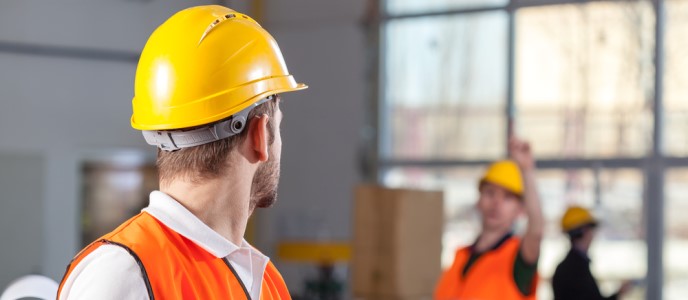
As a small, medium or large business owner, you have a legal duty of care to ensure the safety and health of all workers in your manufacturing workshop, as well as those who come into contact with your business (contractors, subcontractors, apprentices, trainees, volunteers, work experience students, customers and visitors to your workshop).
It is important that your workshop has an effective workplace health and safety system in place that fulfils your requirements under Australian and state law.
While implementing and managing workplace healthy and safety policies and procedures in your workshop and reducing risk can sometimes feel like a business burden, the cost of injuries and illness to your business is significant.
Industries that operate from a workshop environment face the greatest number of fatalities across the workforce and largest total number of workplace injuries and illnesses. According to Safe Work Australia, the business operations cost for a worker who suffers any type of injury or disease from work is an average of $5,800 per incident. This doesn’t even factor in the legal costs should your business not be WHS compliant.
Keeping your workplace healthy and safe doesn’t have to be difficult. The good news is that there are a number of simple steps you can take to make your workshop safe and compliant; reduce work-related fatalities, serious injuries and illnesses; and make business run smoother and more effectively.
Make a commitment to WHS and demonstrate it as a priority.
Effective WHS in a manufacturing workshop requires strong leadership and management. The leaders within your business should lead by example by participating in safety training, wearing protective equipment, following business WHS policies and procedures and leading discussions about WHS with workers. Encourage workers to talk openly about WHS and provide positive feedback if your team follows the principles you put into place.
Understand your WHS requirements and communicate responsibilities with appropriate team members.
Every state has its own WHS regulation body and governing acts and regulations. It is vital that business owners review the relevant legislation to your business so you are aware of your responsibilities. Clearly communicate your business and individual responsibilities to the relevant supervisors, workers and managers within the business. Make sure your workers have the necessary resources, information and training to reduce risk and stay safe in the workplace, and provide the required training needed for people in your business who have specific WHS responsibilities.
Develop a simple, written health and safety policy for your business.
Your policy should state your commitment to WHS, reflect the special needs of your workshop environment and should be regularly reviewed and updated as your business changes and grows. The policy should outline worker, supervisor and business owner responsibilities; accountability of management at all levels; the regular review and continuous improvement process for your policy; the commitment to provide adequate funds and resources; the arrangements (such as regular meetings, education and training) to support and implement the policy; workplace hazards and procedures to address these; and reporting processes. The policy should also incorporate clear guides on maintaining and operating equipment and machinery safely; emergency procedures; and required workplace measures to ensure a safe, risk-free work environment.
Your policy should be written in consultation with the health and safety committee or representatives, or with the workers themselves so everyone is aware of their WHS responsibilities.
Appoint a WHS officer internally.
Consultation with workers to ensure your WHS policy continues to address the risks and hazards of your workshop is vital. As your business grows, consider appointing a first aid officer, fire warden, return to work coordinator and/or health and safety representative who can oversee WHS in your workplace and regularly consult with employees on hazards and risks in the workshop so you can make sure your policy effectively addresses these.
Invest in warehouse safety products.
Your WHS policy should outline the funding in place to ensure your workshop is safe. Investing in quality warehouse safety products, such as anti-slip tape and non-slip tapes, fire blankets, fire extinguishers, industrial spill kits, and other safety products that will keep workers safe, will reduce workplace incidents and any impacts on warehouse productivity.
Warehouse business owners have a lot to think about, so it’s easy to neglect your WHS compliance requirements. The state’s WHS regulator, SafeWork NSW has created a simple-to-follow toolkit for small businesses to make meeting your safety obligations easy. Click here to download the free guide.